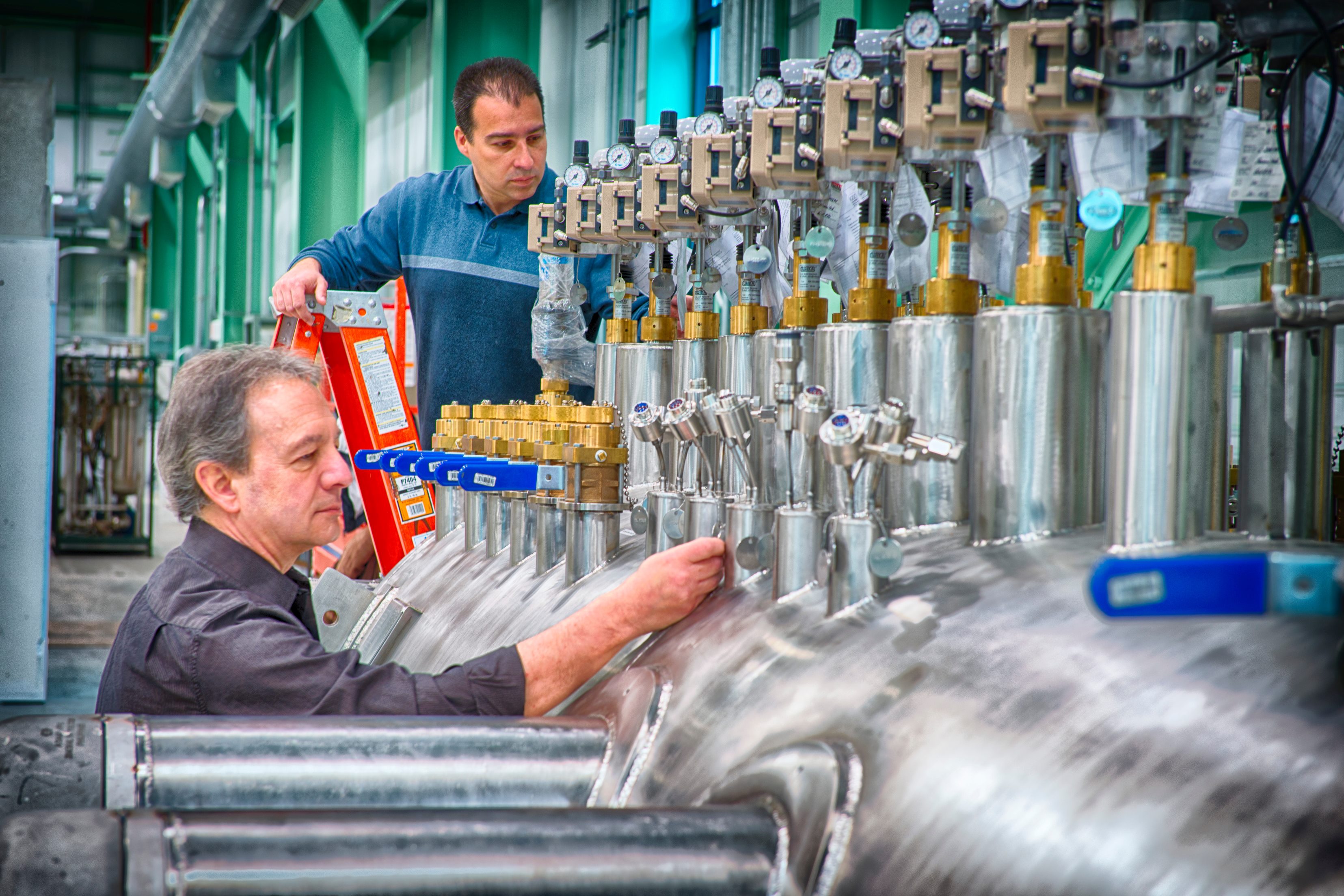
Lean SOPs in Chemicals and Pharma
Lean format SOPs (Standard Operating Procedures) are steadily trickling their way into all sorts of industries
– a tabular layout with instructions in one column and other types of information in additional columns. These are usually labelled Major Steps, Key Points and Key Point Reasons, followed by a column with pictures, diagrams and images.
These formats are probably the best approach to take. They are succinct, informative, easy to read, flexible in how they are read, and capture a lot of knowledge and experience that reduces the learning curve of new personnel. When written well, users’ adherence to procedures increases, reducing variation because users understand the reasons for the exhortations in the SOP and the consequences of failing to follow the SOP. This is information contained in the Key Point Reason column, content typically omitted in most traditional SOPs, or at best inconsistently added.
"a user centric focus"
Within the SOP itself there is no accommodation for extraneous information which is so often added, such as background information, explanation of process and other waffle. This gives the Lean SOP a user centric focus, encouraging a more frequent referral to check details and hence a greater familiarity with the SOP reducing knowledge fade over time.
However, we have seen issues with companies adopting the Lean style SOP. These issues fall into two broad categories;
- A failure to understand how to write an SOP in this format, leading a degradation of the format. This is a lost opportunity to harvest the benefits of a Lean format
- A failure to understand the origins of the Lean SOP and so a failure to adapt to a different environment.
We will deal with the second of these two issues today – we may return to former problem in a later article.
Lean SOPs are part of standard or standardised work, and SOPs are sometimes referred to as Work Instructions or Job Elements. They form part of a suit of documents aimed at making tasks highly repeatable and consistent, easily altered to accommodate reallocation of specific tasks across personnel, and to reflect continuous improvement in production assembly (and other activities).
Within Lean there is a distinct separation between the Engineering Standard and the Standard Work, and the two must not be confused.
The Engineering Standard details the technical aspects of the product. For a car it often matters little about the order tasks are undertaken nor the technique used to undertake the assembly task as a car is blind to whether a wheel is fitted before the dashboard or the other way round. It will, however, have a massive impact on productivity and therefore cost. And so a car company is happy for SOPs to be quickly and freely amended and updated as the SOP will have minimal impact on the technical, so long as everything is eventually assembled in the right location and the bolts torqued correctly.
However, when we translate across into chemical or pharmaceutical settings distant and distinct from automotive we cannot separate out the SOP from the end product – sequence and technique will both have devastating impacts from a chemical and GMP perspective, potentially giving rise to fundamentally different compounds, never mind the potential for catastrophic exothermic reactions. The relatively freer controls of the automotive world give rise to problems in these environments. The traditional Lean philosophy and empowerment of “Just do it” will cause clashes and tension between the technical, quality and process safety departments, and continuous improvement practitioners who fail to appreciate the differences between Lean applied in assembly manufacturing and Lean applied in other industries.
Instead, one has to understand the concepts and principles that underlie Lean SOPs and Standard Work, and to then ask “How do we apply them in this situation; how do we adapt to this environment”.
The equivalent of the Engineering Standard and the Standard Work interact in chemicals and pharma.
One cannot be changed without due regard for the other - changes to SOPs have to consider the impact on the product and process.
This is not to say that personnel cannot be empowered to update SOPs, but controlled management of change (MOC) processes have to be in place and applied to SOPs.