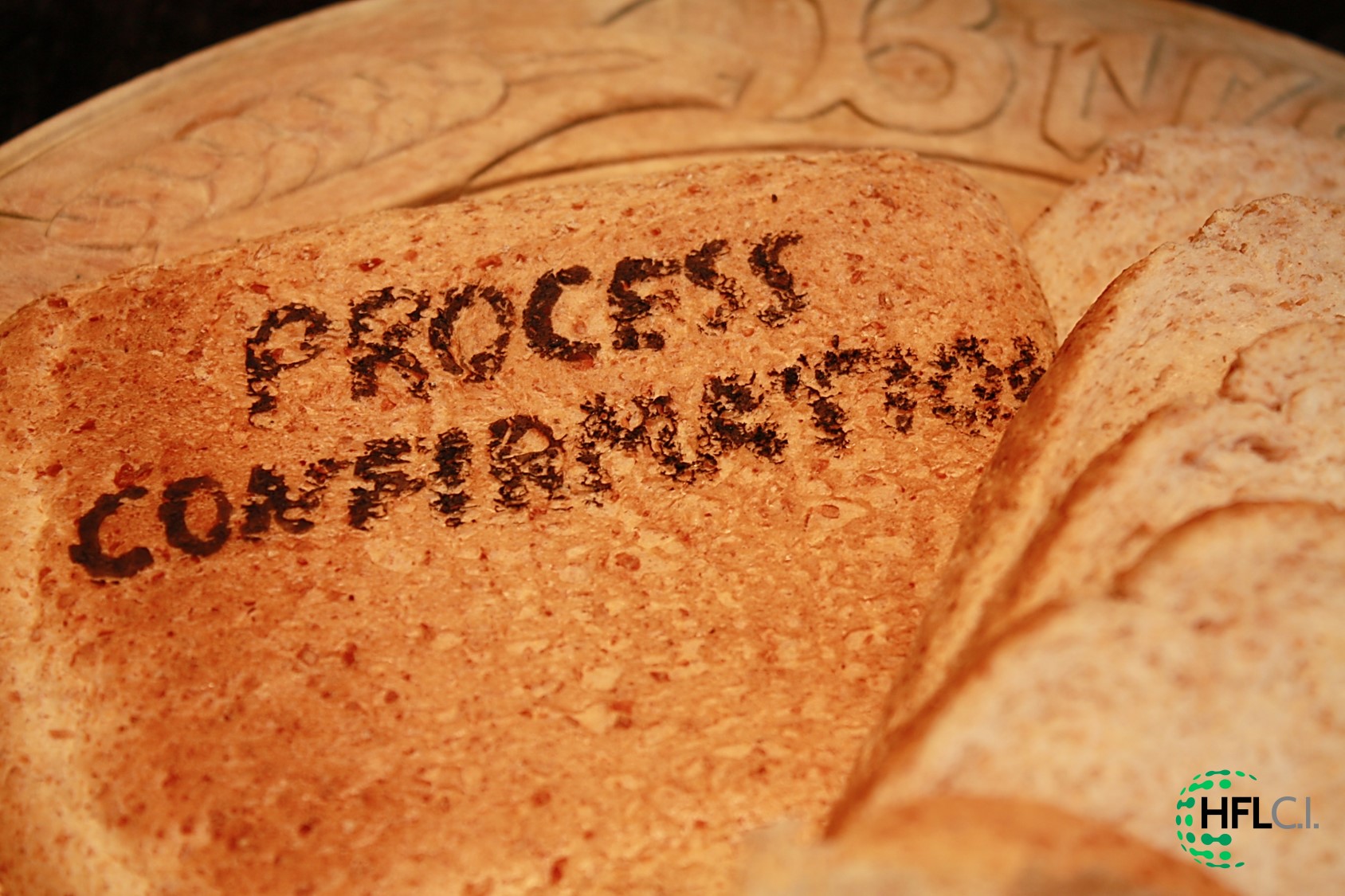
Process Confirmation - The Best Thing Since Sliced Bread
There is a story of Toyota giving a presentation at a conference, where they were waxing lyrical about the benefits and performance of their Toyota Production System (TPS, or Lean as the rest of us call it), when apparently one of the delegates interjected.
“Toyota’s superior performance is because they recruit all the best people, leaving us with the rest”.
The presenter replied
“Our people are the same as everyone else’s. But our systems are better, which is why our people perform better”.
This is a view we share at Haden Freeman C.I. – the environment in which you put people is a strong determinant of performance. The better the systems, processes and procedures your people work to then the better their performance will be. This is why we talk so much about Lean Management Systems, process, and business culture. It matters enormously. Training without these things in place will fail to deliver bottom line improvements – it takes a process to ensure the learning is applied.
Process Confirmation (also known as Tiered Auditing of Layered Process Auditing) is a tool for improving and sustaining business systems. We often think of it as the best thing since sliced bread.
The story goes that Toyota think so too, and at the conference it was quoted as being one of the key tools underpinning their superior plant performance.
Process Confirmation is designed to achieve a number of objectives:
- To sustain and reinforce adherence to critical business systems and desired behaviours to maintain business performance, including safety (process safety and occupational safety)
- To pro-actively discover issues and problems with critical business systems and a site’s culture before an incident or problem arises
- To stabilise operational activities so avoiding a tendency to bounce from one issue and problem area to the next in a firefighting manner.
It achieves this by setting a number of “go look see” and open communication activities between managers and staff. This:
- Leads to first-hand discovering of what actually occurs – work as done vs work as imagined
- Increases the situational awareness of managers enabling them to make better decisions
- Increases the visibility and accessibility of managers, providing opportunities for issues and problems to be communicated upwards.
Process Confirmation forms part of Standard Diaries in Lean– part of setting routine, structure and rhythm to a working day. This leads to increased and balanced focus by personnel, reducing firefighting feedback loops, improved effectiveness in leadership activities, and stability in business operations.
It is a flexible tool able to address a number of issues and problems, and so over time it will tend to expand and grow as it is utilised to address issues as they arise. Indeed, we often refer to Process Confirmation as a solution waiting for a problem to fix.
If you would like to know more about Process Confirmation, the best thing since sliced bread and a solution just waiting for problems to fix, just contact us. We are always happy to wax lyrical on the subject too.