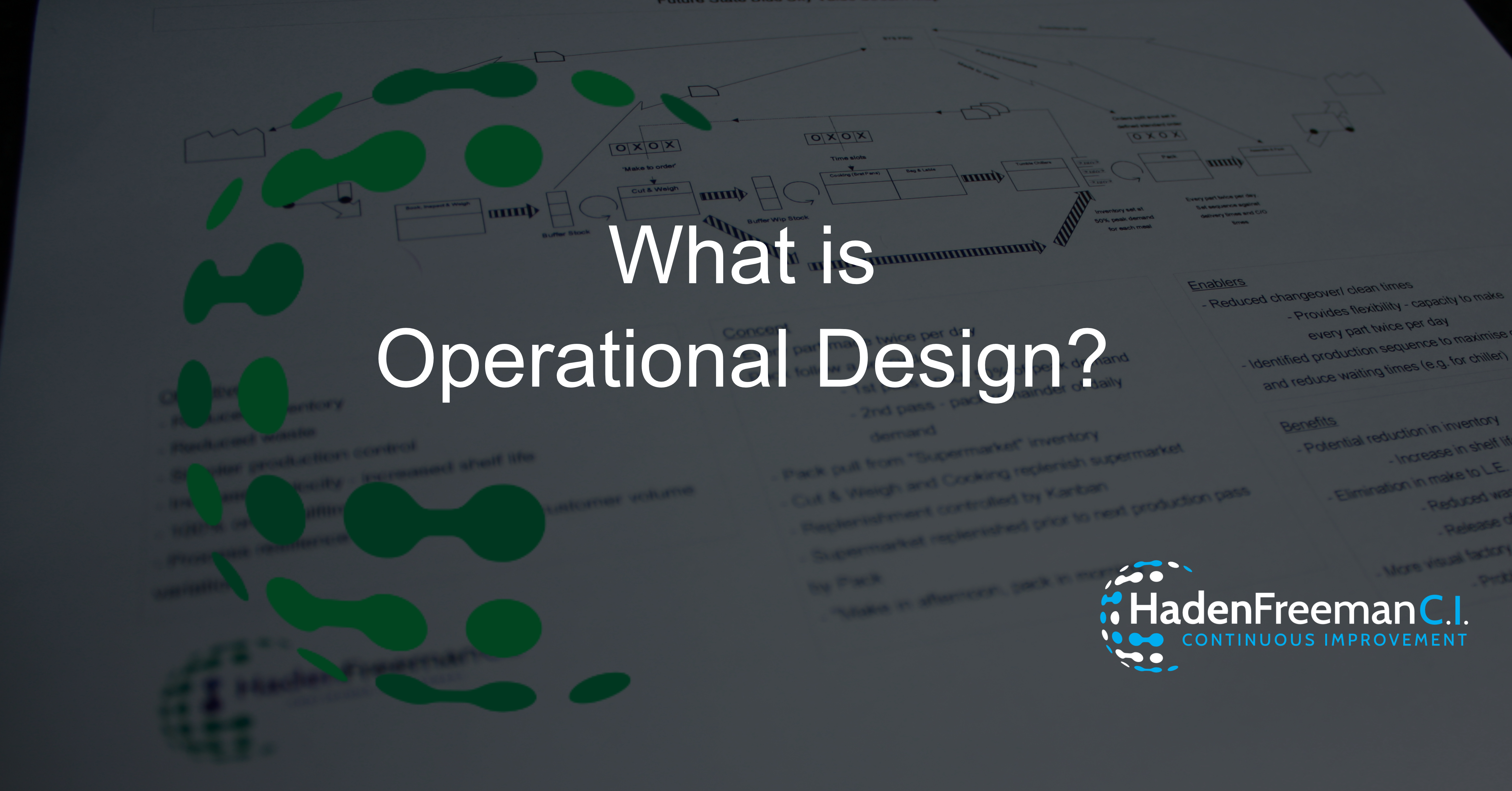
What is Operational Design?
Operational Design is about Integrating a new plant or process into an existing site and supply chain. This allows a new asset to operate efficiently and may be expected to deliver operational improvements and savings to the business wider than the specific bottom line benefit of the newplant.
Operational Design is about thinking beyond the box when it comes to designing a new plant.
By considering the Operational Design or Philosophy (such as campaign or batch sizes, production planning philosophy, changeover times, frequency of deliveries, single piece flow) at the design stage there may be significant opportunities to:
- Reduce production lead times
- Increase capacity for a given cost
- Cut inventory
- Increase On Time In Full (OTIF) deliveries
- Reduce plant footprint
- Increase production flexibility
- Make new plant resilient to breakdowns and outages
- Cut capital costs
Operational Design is the natural evolution of many aspects of Lean tools and techniques.
This can be applied at any point in a plant’s life cycle, and some of the examples below are from applications to mature plants. However, doing so at the initial design stages increases the number and size of opportunities for a lower cost.
Part of the approach is creating a Capacity Model. This will inform design decisions and assess the impact of different Operational Philosophies and other variables such as reliability, changeover times and Overall Equipment Performance (OEE). Design criteria, specifications and design assumptions can be tested for their impact on ongoing operational costs versus initial capital costs.
This can reveal some big opportunities:
- Operational Design and modelling for a drinks manufacturer led to significant capital cost reductions (7 figure saving) and increased operational flexibility giving reduced work in progress and less waste
- Operational Design and inventory holding analysis for a petrochemicals site led to an improved new plant specification which ensured peak customer demands and supply would be met
- A plant layout design and review for a component manufacturer resulted in a fundamental change to their Operational Design dramatically reducing WIP and lead times
- A mapping activity in an FMCG supply chain to assess current Operational Design started initiatives and capital projects that reduced inventory and improved the supply chain leading to multi million-pound savings annually
- A Value Stream Mapping activity for a gas packing site gave rise to a change in Operational Design and stock holding approach which delivered increases in OTIF deliveries and reduced customer delivery times along with reduced production disruption and overtime
How a plant or process is operated has a big impact on throughput, inventory and lead times.
If you are interested in making the operation of your facility more effective, efficient and lean, and potentially reducing the capital outlay for your project, enquire about Operational Design with Haden Freeman C.I.